Melting Device For Die Casting Magnesium Alloy Melting Equipment
Quantitative Pouring System For Die Casting Machine
Melting device
Magnesium alloy furnaces generally use nickel-free (or very low nickel) stainless steel welding or integral casting. Because nickel dissolves in the magnesium alloy liquid, the corrosion resistance of magnesium alloy castings will be greatly reduced.
The crucible is best to have a double-chamber design to separate the melting chamber and the pump chamber to avoid large fluctuations in the temperature of the magnesium liquid, which will affect the quality of the product. When designing the furnace, the surface and volume ratio of the molten magnesium should be minimized. The crucible and the lid should be well matched and sealed.
Quantitative pouring system
Because the smelting of magnesium alloy is carried out in a closed condition. For the hot chamber machine, the material pot and the punching system are also immersed in the magnesium liquid, which can realize the automation of feeding and punching. For the cold chamber machine, a quantitative pouring system is required to pour from the furnace to the pressure chamber of the die casting machine. . At present, the magnesium alloy quantitative pouring systems that have been developed and applied include impeller type, pneumatic type, piston type and so on.
Impeller
The magnesium liquid is lifted by the rotation of the impeller and poured into the pressure chamber of the die-casting machine quantitatively through the feed pipe. The rotation speed and running time of the impeller can be changed to realize the change of pouring volume.
The quantitative accuracy of this magnesium liquid pump can reach ±2%. During production, the stability of the magnesium liquid level should also be controlled to avoid fluctuations in the supply volume. This kind of pump has simple and practical structure, easy operation/maintenance, and low failure rate.
Piston
The principle of the piston type quantitative pump is shown in the figure below. The injection volume of the magnesium liquid can be adjusted by adjusting the stroke of the piston. This kind of pump can achieve higher accuracy in theory, but due to the excessive part immersed in the magnesium liquid. Long-term immersion in high-temperature magnesium liquid makes maintenance inconvenient.

Electromagnetic pump
The electromagnetic pump uses the electric current and the magnetic field in the conductive fluid. The electromagnetic driving force is directly applied to the liquid metal to cause it to move directionally. And its movement conforms to the left-hand rule. The flow rate of the electromagnetic pump is related to the rising liquid current and the magnetic induction intensity.
The electromagnetic pump is characterized by no mechanical wear and convenient control.
Air pump
The main structure of the pneumatic pump principle is a sealed pump chamber. During injection, pressurized argon gas enters the pump chamber through a pipe. The one-way valve connected to the furnace under the pump chamber is closed. And the gas discharges the same volume of magnesium liquid for injection. This pump is characterized by no mechanical wear, low failure rate, simple cleaning and maintenance. And better quantitative accuracy when the pouring volume is large.
Others(1)
In order to facilitate the connection of the magnesium alloy furnace with the die-casting machine, some other devices are needed. For example, the three-dimensional positioning device for the melting furnace of the cold chamber die-casting machine can realize the rotation, translation, and lifting of the furnace to facilitate the matching and daily maintenance of the die-casting machine.
In addition, it is also an important point for magnesium alloy hot chamber die casting machines. Hot work parts such as pots and steel chlorinates. The die casting temperature of magnesium alloy hot chamber is generally between 630℃-650℃. It is much higher than that of zinc alloy. Hot work pieces working in high-temperature magnesium alloy liquid must not only have good high-temperature strength. But also have corrosion resistance to magnesium alloy liquid.
Others(2)
Due to the very harsh working conditions, there are special requirements for the materials used. Magnesium alloy itself is chemically active and has a corrosive effect on the materials of hot work parts. In production, there is corrosion of protective gas. In addition, its high working temperature and high injection speed have higher requirements for the high temperature performance of the hot work material. The research of hot work piece materials for die-casting magnesium alloy furnace has become one of the important factors affecting the development of die-casting magnesium alloy.
Magnesium ingots must be preheated to above 150°C before being added to the furnace. In order to remove the moisture in the magnesium ingot. So as to avoid the danger of explosion when it is added to the furnace. Adding the magnesium ingot after preheating can also avoid causing large fluctuations in the temperature of the magnesium liquid and increase the melting efficiency of the melting furnace.
Therefore, the magnesium alloy melting furnace should be equipped with a holding furnace-type automatic preheating device. And it can also be connected with an automatic feeding device to automatically add the preheated magnesium ingot into the furnace.
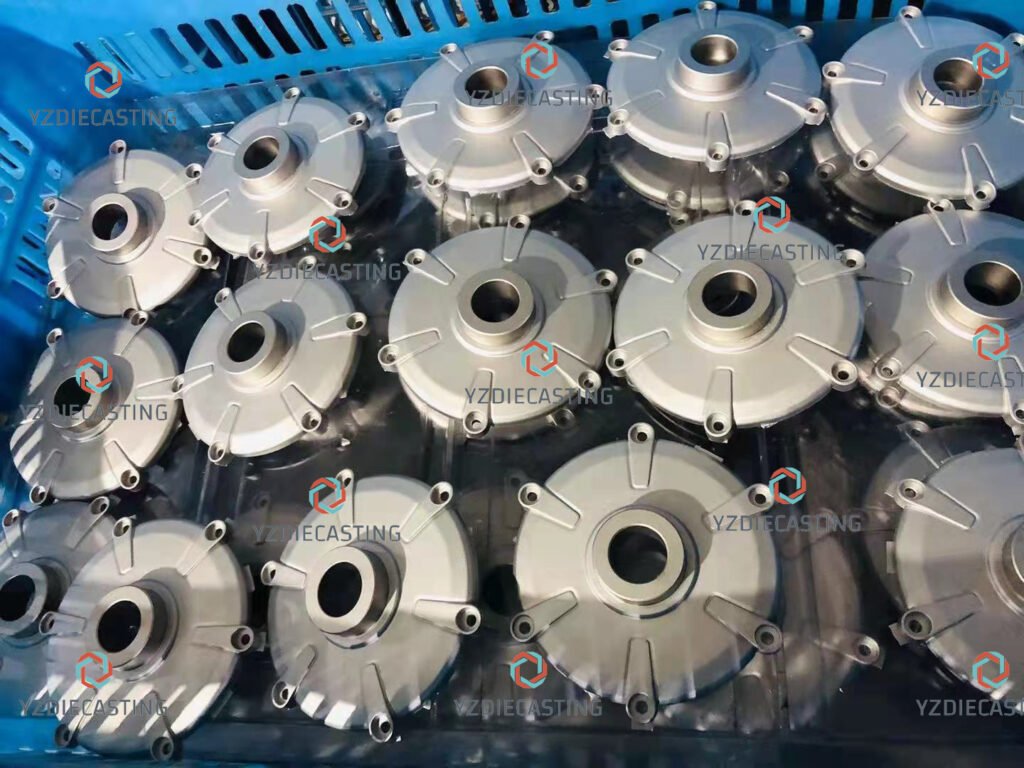