Description; what is aluminum and magnesium alloy die casting? Learn the different types of metals we can use in casting as well as die casting advantages and disadvantages.
What is the exact explanation of Die Casting?
Want to know exactly what Die Casting is? Die Casting is a meaningful term for pressure die casting, many people in the profession call it die casting , a term used exclusively in casting techniques and industry today.
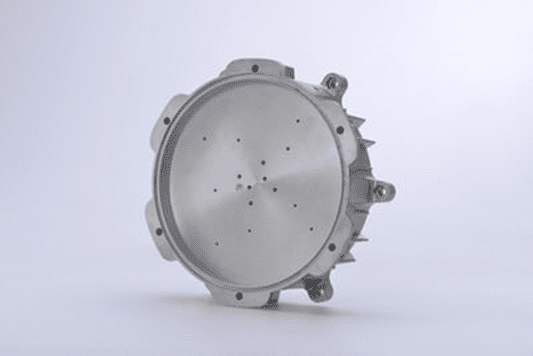
What is the exact interpretation of Die Casting?
Die Casting is simply a technique used by professional companies to manufacture pressure-sensitive equipment such as components in liquid CNC plasma cutting machines or pressure pumps. Die Casting is used to export devices to a specific specification, providing useful features for users.
Die Casting is an extremely efficient way to use, through which the production cost is reasonable and attractive. Moreover, it is easy to apply the technical related parameters manufactured by engineers, technicians. During the Die Casting process, technicians need to monitor, review and perform with many different factors to ensure the process is suitable and balanced according to the standards.
In short, Die casting is a specialized term in the field of casting techniques today; it brings applicability in many different problems of the production process. To better understand Die casting, read the information shared in the next section!
What metal is used in Die Casting?
In the process of Die Casting, which metals and alloys are put into use, let’s find out in detail through the following sharing:
+ Aluminum is the most used and most popular metal in the current die casting process, or it is used in the Die Casting process, but using aluminum is often prone to cracking, or the size will be reduced.
Therefore, very few people conduct pure aluminum casting, but will combine with other metals such as silicon or copper to increase durability and toughness, increase the product’s tolerance in the process of making Die Casting products. .
+ Copper alloy – This is also a frequently used material in the Die Casting process, many engineers have used copper alloy to produce and manufacture high-performance mechanical products. Used a lot because copper or copper alloys have the advantage of effective anti-corrosion, so it is often used to make water pipes or effective electrode conductive materials in the current Die Casting process. .
+ Zinc is a metal that is easily used in the current die casting process. Especially when using zinc in Die Casting process, it will be maintained and more durable because of its high temperature resistance. With zinc’s characteristic of low melting point at high temperature, many engineers/technicians have used the filler metal to perform extremely efficient hot-chamber casting.
Magnesium Alloy Die Casting
+ In addition to the above common metals, in the Die Casting process, Magnesium is also used – This is an alloy with very light force, but it brings high precision to the product during production and application of this type of material.
Basics of magnesium alloy die casting
Die casting of metals is a method of making castings from alloys , in which the alloy takes the form of a casting, quickly filling a mold under high pressure from 7 to 700 MPa. This method is used for non-ferrous alloys (based on zinc, aluminum, copper, magnesium, tin-lead alloy) due to their low melting point, as well as for some steels.
Products can weigh from tens of grams to tens of kilograms. Die casting of metals occupies one of the highest places in terms of volume of mass production in metalworking.
- automotive engine parts (including aluminum blocks, carburetor parts);
- details of plumbing equipment;
- parts of household appliances (vacuum cleaners, washing machines, telephones); earlier – parts of typewriters;
- Parts of computers, mobile phones and other similar equipment.
Application of Die Casting
Aluminum Die Casting: Used in lightweight and high strength assemblies; gearbox housing, etc.
Magnesium die casting: used in light and high strength assemblies, for example: electrical equipment housings.
Zinc die casting: used in the manufacture of toys and in small parts, as well as in assemblies with good surface quality, especially where there is chrome plating.
Die casting brass: used in sanitary ware such as water taps, faucets.
Product Manufacturing Process
Casting molds are usually made of steel. The shape of the mold cavity is chosen to be similar to the outer surface of the casting; however, dimensional distortions are taken into account.
The mold also contains ejectors and movable metal rods that form the internal cavities of the products. Foundry machines divided into two types:
- with a hot
- cold pressing chamber
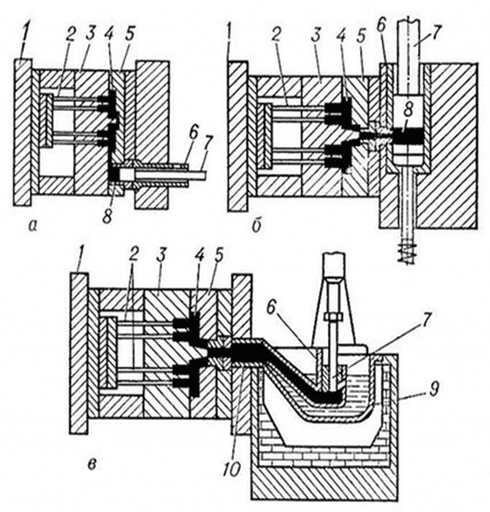
Schemes of die casting on machines with bale chambers:
a – cold horizontal; b – cold vertical; in – hot; | 1 – plate for fastening the movable part of the mold; 2 – ejectors; 3 – movable mold matrix; 4 – mold cavity (casting); 5 – stationary mold matrix; 6 – pressing chamber; 7 – pressing piston; 8 – press residue; 9 – crucible of heating transmission; 10 – Heated mouthpiece. |
Hot chamber casting machines
Zinc alloys are generally cast in hot chamber machines. The chamber is immersed in the melt. Under a relatively weak pressure of compressed air or piston, the melt is forced out of the chamber into the mold.
Key features:
- High-speed operation. Cycle times less than 1 second for small parts, up to 30 seconds for larger parts.
- Working pressure in the range from 100-300 atm.
- Conventional presses or small high-speed machines.
Cold chamber casting machines
Such machines are used for die casting of aluminum, magnesium, copper alloys. Casting into molds takes place under a pressure of 35 to 700 MPa.
Key features:
- The injector plunger and cylinder will not sink into the molten.
- The molten metal is poured with a ladle mechanically or manually.
- Longer cycle times. It can be up to 1 min.
- Working pressure 200-700 psi Al and Mg (13-47 atm.).
- Working pressure 400-1000 psi Cu (27-68 atm.).
Aluminum die casting
Aluminum die casting is a technological process that ensures high quality of thin-walled products of various shapes and configurations, which practically does not require further mechanical revision.
You can get castings with internal or external threads, various channels and cavities, wall thickness from 0.5 to 5 millimeters. The weight of products can range from a few grams to tens of kilograms.
What is aluminum die casting today?
Modern processes of die casting of aluminum alloys are distinguished by full automation of production, high productivity and perfect accuracy of the linear dimensions of the manufactured products.
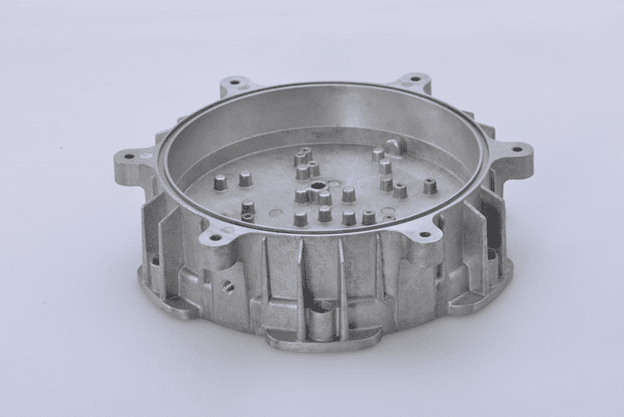
The CNC unit sets the necessary modes, parameters and methods of casting:
• temperature regime of raw material melting;
• pressure and speed of melt injection;
• cooling time of finished products.
Fully automated process eliminates staffing and overhead costs
Models of die casting machines differ:
1. Productivity – this indicator determines how many parts a machine can produce per hour.
2. Equipment dimensions. The choice of production facilities depends on the size and weight of the machines.
3. A lot of castings. It depends on the equipment of the machine: pump power, motors, sizes and types of molds.
Why is pressure used in aluminum casting?
Due to the high injection speed under pressure from 35 to 700 MPa, casting with precise detailing of products is possible.
Advantages of die casting :
• possibility of casting products with the thinnest walls;
• compliance with all necessary parameters of castings;
• no waste;
• perfect surface quality.
Die casting into molds – the ability to obtain serial products for various industries, mechanical engineering, medical and food industries.
Finished products do not require mechanical processing, which saves raw materials.